Troubleshooting Process Operation
Develop troubleshooting skills for efficient process operation. Enroll in this course to learn techniques for identifying and resolving operational issues.
City | Start Date | End Date | fees | details |
---|
Introduction
Delegates will learn and review the core competencies required for successful operation and implementation of an effective operations process in the current global economic downturn. They will complete an in-course assignment, which analyse their own process operation and which will serve as an action plan for improvement.
Objectives
Participants attending the programme will:
- Gain a broad understanding and appreciation of the core functional aspects of how an effective operational process should operate
- Review the five standard maintenance improve tactics and their selection technique to ensure reliable process plant & equipment
- Learn how to develop a comprehensive operational process resource and support system analysis
- Understand the principles of PAS 55, the most recent maintenance process audit standard
- Gain insight and understanding into the unique leadership and motivation principles required for technical management
The Contents
Day 1 - Review of Basic Modern Operations Practice
- Review of modern operational practice in the light of the global economic recession
- Integration of maintenance and production to establish a world class operations department
- Generic performance measurement model using a 6 point scale
- Combining the parameters of speed; quality; and cost; in maintenance performance measurement
- The 10 point planning standard and the role of the planning department
- Developing effective strategies for the operational process in order to achieve organizational excellence and continuous improvement
Day 2 - Standard Maintenance Improvement Initiatives
- Selecting the ‘correct’ maintenance tactic mix
- Reliability Centered Maintenance (RCM)
- Total Productive Maintenance (TPM)
- Condition Based Maintenance (CBM)
- Time Based Maintenance (TBM)
- Run-To-Failure (RTF)
Day 3 - Operational Resource Analysis
- A ‘blueprint’ for effective operational practice
- Resource and support system analysis with ‘Gap Analysis’
- Leadership development and motivation of operations employees
- The PAS 55 Maintenance Process Standard
- Principles of information management
- Risk identification, assessment and control
- Training, awareness and competence
Day 4 - Problem Solving in the Operations Environment
- Theory of inventive problem solving
- Problem solving techniques and case studies
- Exercises and facilitation
Day 5 - Scenario Analysis and Action Plan Development
- Review and analysis of your specific operations environment
- Assessment assignment and scoring of your operational process
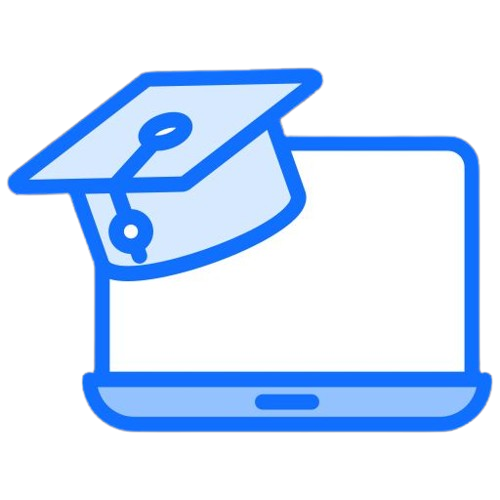
Code : MAE5
Data Analysis Techniques
One Week
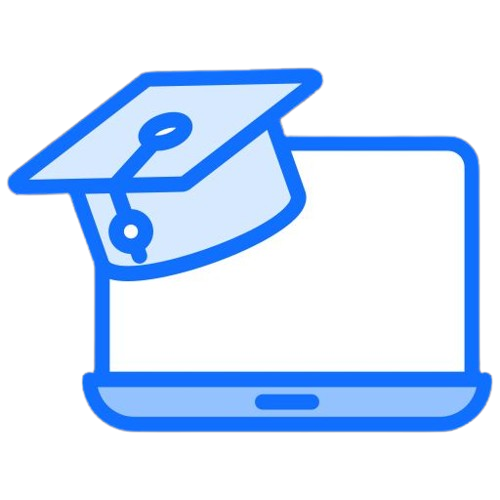
Code : MAE8
Fluid Flow and Heat Transfer in Industrial Applications
One Week
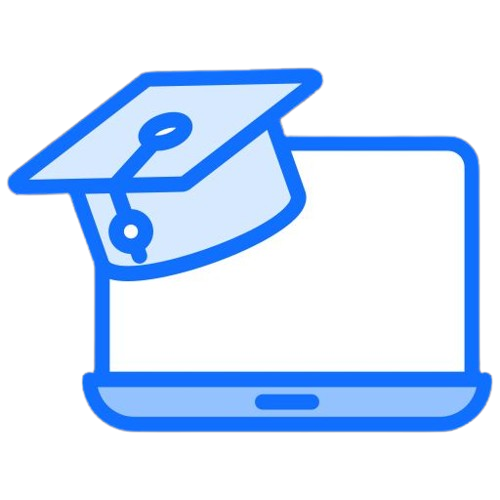
Code : MAE15
Maintenance Strategy Development and Cost Effective Implementation
Two Weeks
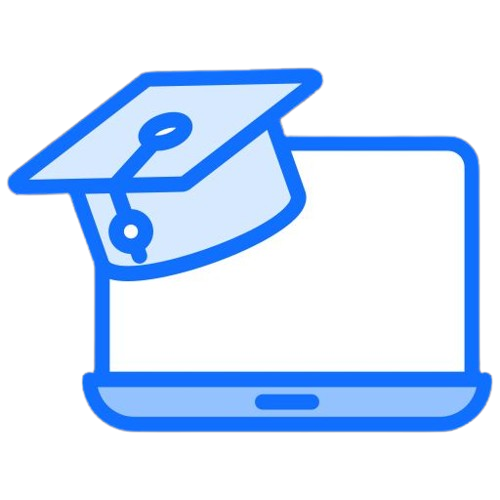
Code : MAE18
Metallurgy for Non Metallurgists
One Week
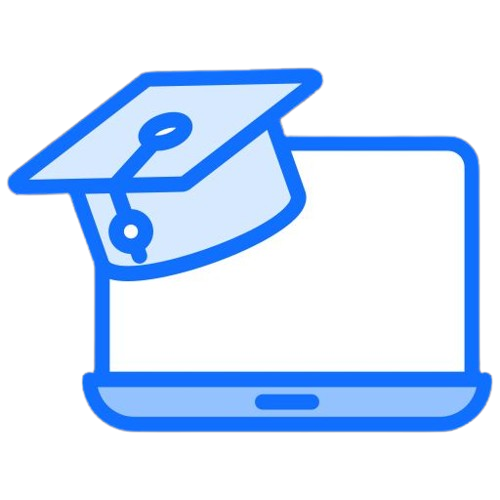
Code : MAE29
Root Cause Failure Analysis
One Week
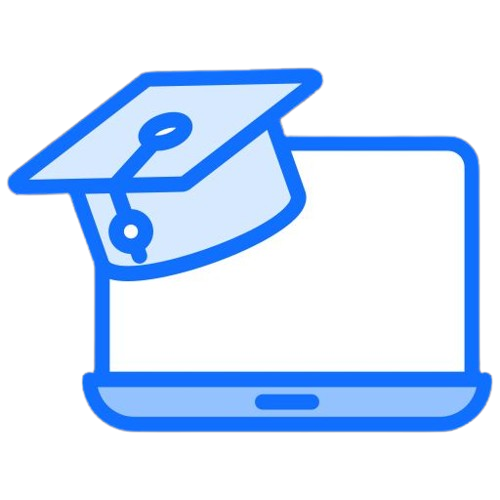
Code : MAE33
Troubleshooting Process Operation
One Week
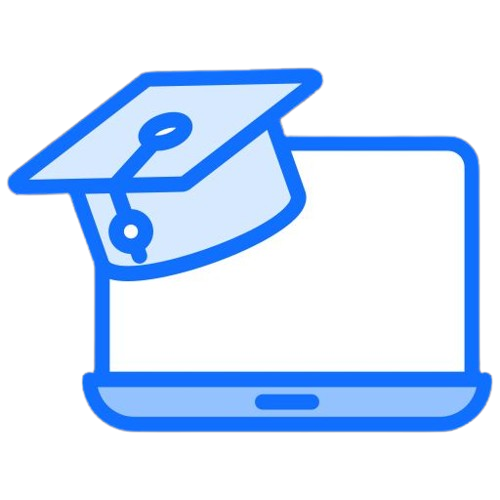
Code : MAE40
Maintenance and Reliability Best Practices
One Week
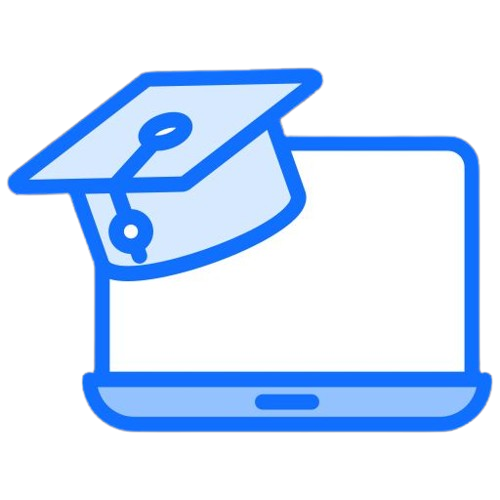
Code : MAE41
Maintenance Contracting and Outsourcing
One Week
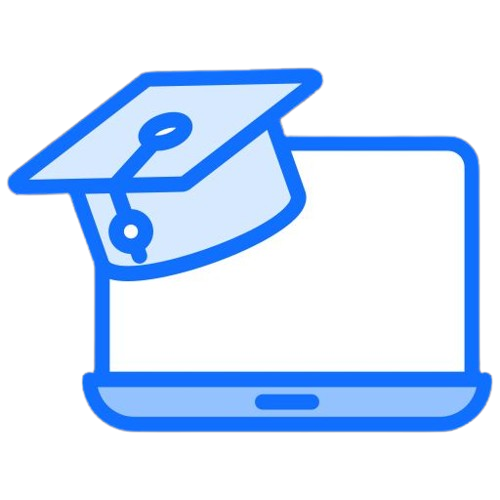
Code : MAE45
Optimizing Equipment Maintenance and Replacement Decisions
One Week
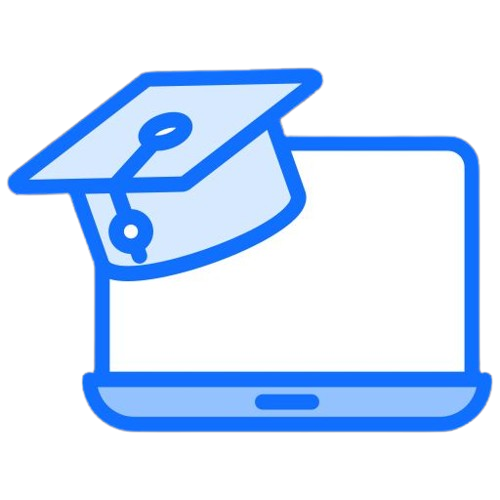
Code : MAE47
The Complete Course on Maintenance Planning and Scheduling
Four Weeks